How Integrated Facilities Management and Robotics Are Reshaping Healthcare
- SIMPPLE
- Nov 16, 2021
- 4 min read
Updated: Jan 31, 2024
In the dynamic landscape of healthcare transformation, discover how SIMPPLE's integrated facilities management software and robotics is spearheading change in the healthcare industry. In Singapore alone, SIMPPLE’s suite of technologies is deployed in over 400 buildings equipped with 3000 sensors, empowering more than 2000 human and robotic assets. In the short span of 2 years, we gathered more than 10 million data points and we are looking to grow exponentially between 3 to 5 times across continents by 2023. In order to see such growth, we need to look beyond only the environmental service industry, but to also tap into other industries, e.g. healthcare, which can benefit from SIMPPLE.
With rising utilisation and higher manpower costs, it is inevitable for healthcare costs to increase over the next few years. Information technology will play a crucial role in relieving some of these pressures faced by the healthcare sector with solutions such as wearable trackers and Telemedicine. SIMPPLE will serve to provide solutions that can best support the healthcare industry.
Contrary to popular belief, automation was not introduced as a means to replace people and human labour, but rather to work alongside human labour to boost overall workplace productivity. SIMPPLE believes in the harmonisation of hardware and “heartware” and introduces a series of automated hardware that is “by the people, for the people” in an attempt to help the team perform better safely and generate higher value.
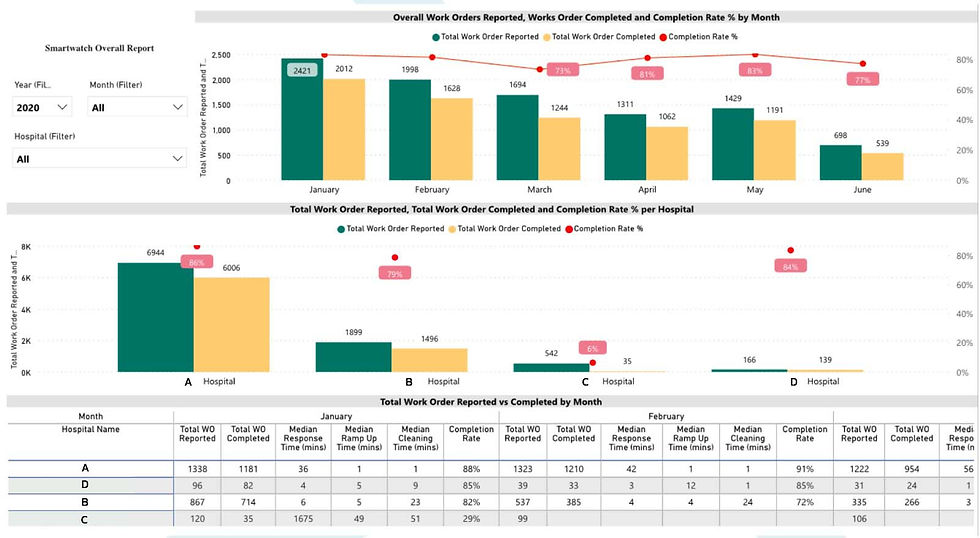
Quality Audit System
The Quality Audit System (QAS) is a real time audit system that allows supervisors to conduct checks of cleaning quality virtually and provides valuable insights to operational challenges and trends, facilitating management decision making processes.
The implementation of the QAS has seen an elimination of paper usage in the team’s workflow. With data analysis and trends prediction, recurring problematic areas can be identified and specific re-training could be carried out for individuals, to improve their work output.
As a result, the number of retouch-ups needed to be done has dropped significantly (from 288 re-touch- ups to 24 re-touch-ups within a 8 month period). The amount of time spent for manual audit report has also dropped to 0, since reports are generated automatically via the backend once the audit report is submitted. Response time for retouch-ups have drastically improved, since staff can be notified immediately if any follow up actions are to be carried out.
This translated to over 280 man-hours saved monthly. Room turnaround time has also improved drastically. The collation of data also provided insights to existing cleaning practices, forming the basis of re-designing of cleaning methodologies, training programs etc.
When the project was first implemented the hospital and SIMPPLE had initial concerns of a slow take-up rate transiting from conventional audit medium to the QAS. However as operational staff are involved at an early stage of the project, the Graphical User Interface (GUI) has been optimised for ease of use, allowing for a seamless transition within 2 weeks.
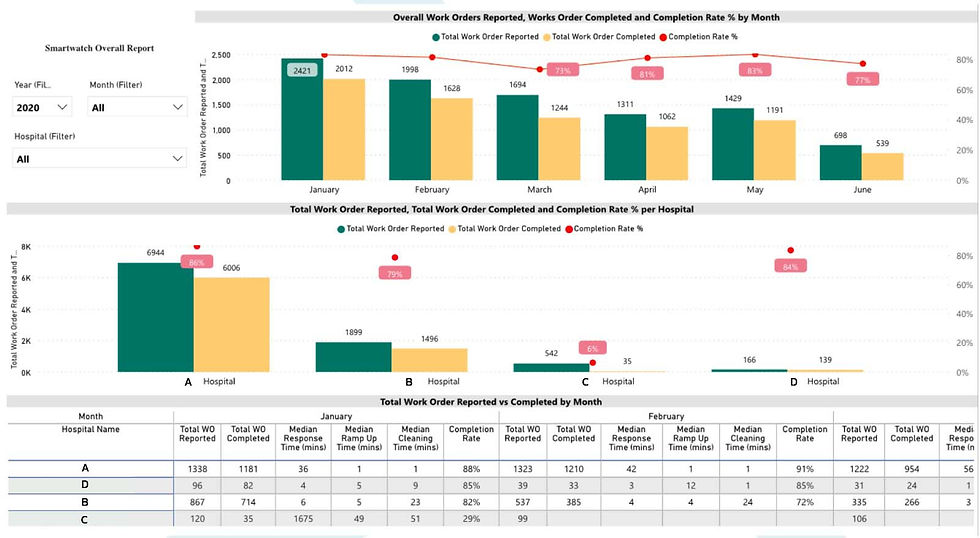
Workforce Management System
The Workforce Management System (WFM) is a cloud based resource management system that enables real-time tracking of work status feedback, and offers a seamless platform for scheduled and ad-hoc work order processing.
The data is captured within the same platform within the same digital eco system to enable individualised performance benchmarking and assessment. This system was introduced with the aim of enabling resource levelling and allocating tasks as per schedules and ad-hoc occurrences based on their respective priorities. This system operates on a series of complex algorithm which assigns work orders automatically based on the operative’s relative location, job loading and pushes the work order to a Global Positioning System (GPS) enabled smart watch for acknowledgement by the operative.

Smart Toilet System
Smart Toilet involves the retrofitting of existing toilet with passive sensors (such as infrared, ultrasound, ammonia, proximity) to monitor human traffic, ammonia levels, inventory and bin levels in real time. This system was introduced in an attempt to shift from conventional schedule based cleaning to a demand based one such that operatives can be freed to carry out other higher value tasks.
The system is linked to the QAS which will send out tasks to cleaners when any of the set threshold has been met. Data collected will be used for trend prediction and aid supervisors in making business decisions in the future. Like the QAS, the platform enables individualised performance benchmarking, assessment and re-designing of existing cleaning methodologies.
On weekdays where the toilet was more heavily utilised, up to 14 cleans were scheduled by the system, while weekends and days with low patient census had less than half that amount at 5 cleans. While the toilet cleaning increased by 20% during peak hours in the weekdays, a manpower savings of up to 90% was observed for non-peak periods. These data allowed management to channel resources effectively to optimise resources deployment while not compromising on standard of cleaning.

All in all, the implementation of SIMPPLE's smart building software and robotics at the hospital saw to higher productivity levels, greater cost savings and elimination of unnecessary operations all while maintaining, and even improving, the clean quality.
Join the hundreds of businesses who are already leveraging SIMPPLE’s Smart IoT solutions to improve their building and facility operations today.
Comments